CD Automation can provide its knowledge and its specialists for the following applications

Flat glass production
SCR units for flat glass production lines, tin bath, annealing glass

Glass tempering plants
SCR units for glass tempering furnaces

Rolling and bending plants
Multiple SCR units up to 24 channels with fieldbus
CD Automation is specialised in this type of application, supplying the complete cabinet package including the Thyristor units. With its own technical department, CD Automation can study the process & system, produce the hardware & software, fully commission the start up process and provide a first class service during the Float Life.
Typical cycle for Glass Industry with Profinet/Ethernet IP/Modbus TCP communication
Typical systems can have between 30 and 35 zones, each one having a power range from 100 to 150 KW. CD Automationproduct normally used is REVO C-3PH. Here on the side you can find an example of a controlled area via fieldbus. For each zone it is possible to have a dedicated terminal to be positioned in front of the panel, connected directly to the unit. In the event of an emergency it is possible to operate on the unit by setting its power in manual mode with prior knowledge of the password or enabling from the control room. In the Tin Bath part the SiC silicon carbide elements are placed on the secondary of a transformer, while in the Annealing Lehr part it is a question of controlling normal three-phase connection resistances, in this case you can choose between the REVO C series and the REVO S series 2ph.
In addition CD Automation can offer REVO PC: This powerful unit with its unique algorithm will minimize energy cost by controlling synchronisation and power limit of each zone. CD Automation can also supply product and specialist know how for the following applications in the Glass Industry.
With the tempering process, the glass is treated with heat to make it stronger and more resistant to high temperatures. The hardening means that, in the event of damage to the glass, damage to people is minimized. Tempered glass is found in the entrance doors, in the shower stalls, in the stoves and in all those applications where a solid and safe glass is needed. Static units are used in the part of the glass heating process. Given the low temperatures, the elements used are simple resistances. The most used products are those of the REVO S series with logic input, with load and SCR junction diagnostics. Also functions that allow more data on the process variables via fieldbus are increasingly required. For this reason the evaluation of the REVEX, REVO C and REVO PC series is recommended.
Together with the tempering process of the glass, which makes it safer in case of breakage, the lamination process takes place. This process consists of the union of several layers of glass with a film of plastic material. In case of breakage of tempered glass the broken parts will not fall on the people, but the fragments remain attached to the plastic sheet minimizing damage to people. Together with this process, which is widely used in the production of windscreens, rear windows and car windows, the process of bending and screen printing of glass is often found.
With the thermal tempering process the bending furnace is heated up to temperatures between 650 and 750°C until a fairly viscous slab is obtained and to make it adhere to a concave or convex mold positioned inside the machine. A cooling phase follows, in which the glass remains compressed in the mold.
For these processes normal resistors are used, they are processes where the required precision is very high in power control. Units are often required that can control power very accurately both in phase angle and in single or half cycle ignitions. Therefore the use of REVEX, REVO C or REVO PN units is recommended
CD Automation Static Units can regulate the power in the following applications, which make use of Heating Elements:
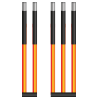
Silicon Carbide elements
Electric convections ovens, Laboratory melting furnaces (temperature up to 1500°C), Glass melting furnaces up to 1350°C, Flat glass manufacturing (Tin Bath).
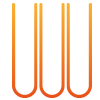
Kanthal Super Elements.
High temperature furnaces (from 1600°C to 1800°C).
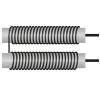
Normal resistances.
Ovens with radiation or convection heating; Continuous ovens; Chamber furnaces; Basin ovens up to 900°C; Glass tempering furnaces; Glass annealing furnaces; Windshield forming; Car glasses; Glass lamination.
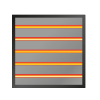
Infrared lamps.
Fusing furnaces; Furnaces for decorations; Ovens for cooking flat glass prints and glasses; Baking decals on glass; Glass fusing furnaces up to 1000°C; Glass silk-screen drying; Glass lamination and tempering; Solar cell production lines (metallized and diffusion); Photovoltaic module production lines (Preheating and stringing); Thin film production lines in preheating lines.
Silicon Carbide elements (SiC)

Silicon Carbide is a semiconductor material, and has a much higher resistivity than metallic resistance materials. Room temperature resistivity is fairly high, and falls with increasing temperature to a minimum value at about 600-900°C. At elements temperature above 900° C. Resistivity increase with rising temperature, as shown in figure.
Therefore a constant power regulation is required with a V-type feed back to VxI transfer. On three-phase loads with Silicon Carbide it is suggested to use a feed back in VxI to obtain a constant power regulation. This is necessary to compensate for changes in the resistance value with the temperature and age of the elements. The value at the end of their use is 4 times the initial value. With the REVO C series use Burst Firing and power limit.
All silicon carbide elements gradually increase in resistance during their life in operation and the rate at which this occurs is affected by the following factors:
a) Element Specific Loading
b) Operating Temperature
c) Process Atmosphere
d) Mode of Operation (continuous or intermittent)
e) Power Supply Type used
f) Element Type
To optimize element life, the right type of element should be selected and the lowest specific loading consistent with the fournace design should be used. To compensate for the gradual increase in element resistance (ageing), a variable voltage power supply is usually provided, to enable the design power to be maintained throughout the life of the element.
MoSi2 Heating Elements
(Kanthal Super®* Elements)

This kind of heaters increase resistivity sharply with temperature.
The graph in this page show that at ambient temperature the resistance value is very low and increase its value up to 10 times.
To don’t oversize in current the Thyristor unit it’s necessary to limit the current to the load reducing the voltage with phase angle firing and current limit.
When the resistance value reach a setted value are possible two types of working method that can be selected from HMI:– Phase Angle plus current limit all the time long Or– Phase Angle plus current limit when the resistance is cold and transfering to Delayed Triggering if load is coupled with transformer.
*Registered Trademark of Sandvik Corporation
Normali resistances

Select your load connection:
Pure resistive load
In this application REVO S Family up to 700A is normally used. Over this current we recommend the REVO C Family, up to 2100A. REVO C Family is also appreciated for communication, voltage compensation and burst firing, which prevents fluctuations in the mains voltage.
REVO PC is used to avoid Power Peak and Enegy Saving.
Load on secondary of transformer
Transformer have inrush current on start up. Special Tyristor Power Controller are required. REVO C with current limit option is normally used for 1PH loads. REVO C-3PH is used for three phase transformer.
Infrared lamps

Infrared radiation is commonly used for many industrial production processes. In secondary glass processing, infrared radiation is used for localized, fast and direct heating. This type of heating has a high penetrative efficiency, is easy to control, requires few costs, and is easy to install and maintain. From the point of view of lamp control we have the following cases:
Infrared lamps Medium and Long waveform
This type of heating elements are controlled as a normal resistance load, providing that the nominal supply voltage is used. If using medium waveform at a lower voltage than nominal, then this should be treated as short waveform load.
Infrared lamps Short waveform
Infrared Short Wave loads can be driven with different types of Firing: Single Cycle, Burst Firing and Phase Angle with Current Limit.
The graph demonstrates how the inrush current remains high for a longer period if we use Phase Angle plus Current limit, than with Single Cycle. Single Cycle technique is the most used to drive infrared short waveform. During the Off time the IRSW elements become cold (due to their low inertia) and when switched ON again there is a peak of current. This peak of current is a function of the number of Burst Firing Cycles, for this reason the Off time must be as short as possible to reduce this current peak. Phase Angle firing is not used because the supply voltage is normally less than nominal and therefore the elements never reach the working temperature.
CD Automation is a 100% Italian company, was founded in 1987 and thanks to its thirty years of experience in the sector produces thyristor power units of the highest quality, intended for automation.
The main office is in Legnano (MI) with over 1500 square meters of offices and production, a qualified team in Italy and abroad with distribution in over 32 countries, with a production site in India and a commercial office in the UK both owned.
We design, manufacture and distribute intelligent electronic devices for electrical power control all over the world to optimize the operation of electric heating systems for large civil and industrial plants.
